With the project ending in September 2022, FLOWER enters its final phase, with the three planned demonstrators being in validation.
The bill of specifications planed the conception of three innovative prototypes for the advertising, nautical and automotive sectors. The main objective was to create sustainable, cost effective and environmentally friendly lightweight composites, using locally cultivated flax fibers. All project partners participated in the making of these biocomposites, by the supply of flax fibres, the conception of semi-products (EcoTechnilin, TVDC), the production of prototypes (Howa-Tramico, Kaïros) and mechanical tests of these new materials (UBS, INRAE, UOP, UOC).
The work carried on to finalise these demonstrators is presented below:
Automotive headliner – Howa-Tramico (WP T1 – T2)
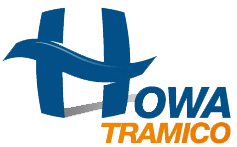
The initial objective for this prototype was to develop and produce a new automotive headliner with an improved environmental assessment thanks to the use of plant fibre reinforcement instead of glass based ones.
The developments of Ecotechnilin in the framework of Flower project led to the manufacturing of new light-weight flax fiber reinforcement which includes oriented and selected flax fibers. The latter was used by Howa-Tramico to develop the new headliner part detailed bellow. Until now, this type of reinforcement did not exist on the market. To manufacture the final part, a thermoforming process is used and then some specific finishing operations such as cuttings.
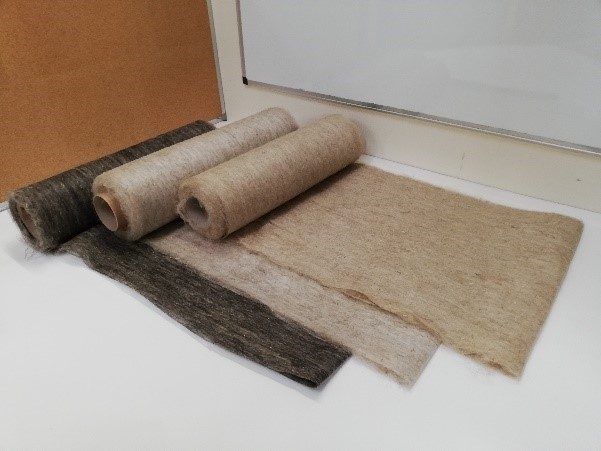
In order to use the veil developed by EcoTechnilin, different validation tests were performed all along the project and a final version of the web was recently finalized, with nice homogeneity, easy to hand and having a suitable arela weigth.
UBS and INRAE developed specific characterizations to better understand and improve the properties of the new products we develop. For example, interfacial properties between flax and our resins were investigated, as well as the microstructure of the parts or the specific location of the resin in flax fibres or foam we used.
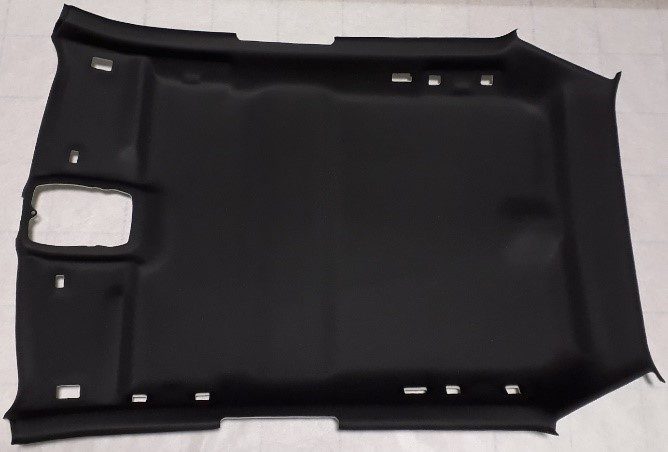
After complete validation of the flax web properties, headliners at scale 1 were produced. It is interesting to note that the integration of light flax web was performed without any modification of the existing process. The prototypes newly produced are innovative and of great interest for Howa-Tramico in a framework of green transition and evolution of the company products towards more environmentally friendly solutions.
During the product development, a Life Cycle Analysis (LCA) – by “Cradle-to-Gate” approach – has been carried out to evaluate the environmental impact due to the replacement of glass fibers by flax fibers. The results shown a decrease of impact on all studied environmental indicators (Between 4% and 32% depending on indicators). This analysis confirms the interest in the use of flax.

Kairlin Point of Sales – Kaïros (WP T1 – T2)

For the advertising sector, the Kairlin® was developed by Kaïros. It is a 100% natural and elegant biomaterial, recyclable and compostable, allowing packaging, point-of-sale (POS) and signage displays to be produced and recycled with reduced environmental impact, in line with the circular economy approach.
Most materials used in the POS, advertising and signage sectors are made from non-renewable resources. They offer a light weight and high surface finish allowing printing, serigraphy and machining. However, the major issue of these solutions comes from their non-renewable origin and their end-of-life which generate a high environmental impact. It is still difficult to recycle them and their production requires a high energy consumption.
The Kairlin® was developed to fulfill these same specifications but above all to reduce the environmental impact of the conventional materials by using biocomposite technologies made of renewable and recyclable/recycled raw materials.
The first step consisted of creating with Ecotechnilin a new flax fiber non-woven reinforcement, competitive with existing products. This new reinforcement not only guarantees better specifical mechanical properties but also allow manufacturing of light bio-composite panels. This innovation is a major advance for the non-woven applications in terms of weight, energy savings and optimisation of reinforcement architecture.
The second step was to develop a process that would use this new reinforcement and that will match the entire POS specifications. This led to develop a new thermocompression which is today patented and that allow to produce the first large bio-composite panel ever made with mirror surface finish and matching.
The new panel has been tested and validated by professionals of the printing and POS industry in order to confirm that the new material matches with both theorical specifications and practical processes and uses of the industry such as machining, shaping, printing and assembly.
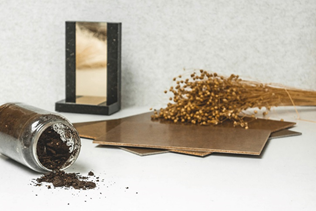
Besides, characterization studies have been carried out at different stages in collaboration with the University of Portsmouth and the UBS. These studies have validated the mechanical, dimensional and environmental properties of the biocomposite panel. In collaboration with Kaïros, UBS has especially carried out a life cycle analysis (LCA) highlighting, in support of a series of feasibility tests in the laboratory, different viable recycling scenarios for these POPs (extrusion, injection, 3D printing).
Birdy Fish Boat – Kaïros (WP T3 – T4)

Finally, the last prototype, also developed by Kaïros, is linked to the nautical sector with the making of a foil sailboat, whose hull and deck are entirely reinforced with flax fibres.
Until now, these flying boats have mainly been made of high performance composite materials integrating carbon and glass fibres. The challenge is to show that natural fibres, less damaging for the environment, can also be used in the making of a foil sailboat.
A first work was done by TVDC to develop multiaxial preforms. UBS and UoPlaobratories then carried out mechanical and vibration tests to validate that the bi-axials are technically suitable for the mechanical stresses experienced by a ship of this type.
After validation and conception of the fabrication plans, Kaïros used these preforms with the company Birdy Fish, who develops boats with the same name, made until now of camposite from glass fiber, polyester resin, PVC foam and non-woven polyester (Soric).
Two parts of the sailboat were chosen to incorporate natural fibers: the hull and the deck, made from two different toolings and requiring two different methods of fibre integration. The hull and deck were made by Kaïros in the PIV Composites facilities (La Merlatière, 85).
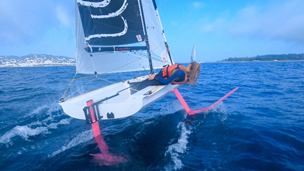
All the parts were then assembled and the first sea trial of the yacht will take place in March 2022. Ageing and sailing checks will be carried out until June 2022 for finalisation. The boat will then be tested in real conditions of use for at least one season at the Glénans sailing centre.
On April 21st and 22nd, FLOWER partners will discover the boat during the last Steering Committee Meeting held in Concarneau.